Machine Safeguarding Services
Annual Safeguarding Validation Audit
Annual validation audits are crucial for ensuring that machinery is properly safeguarded, helping to reduce the risk of operator injuries and prevent costly accidents that can lead to expensive repairs, regulatory fines, increased insurance premiums, and financial strain on the company.
Ensuring Ongoing Safety with an Annual Validation Audit
Customized Safeguarding Solutions for Over 50 Years
Since 1971, Rockford Systems has provided tailored safeguarding solutions to help businesses of all sizes meet OSHA regulations and ANSI standards, protecting both employees and machinery. With over 10,000 safeguarding products, we offer comprehensive services such as risk assessments, machine safeguarding evaluations, emergency response, and training to keep professionals informed on the latest safety regulations.
Our extensive experience has shown that machine safety is a continuous process, which is why we offer our Annual Validation Audit (AVA) to identify compliance gaps and protect your investment in safeguarding equipment. This audit helps address deficiencies and demonstrates a proactive safety approach to OSHA and other regulatory agencies. Large organizations often conduct audits multiple times per year, recognizing their business value and impact on overall safety.
Is an Annual Validation Audit Right for You?
If you answered “yes” to one or more of these questions, it’s time to schedule an Annual Validation Audit to ensure ongoing safety and compliance.
Benefits of the Annual Validation Audit (AVA):
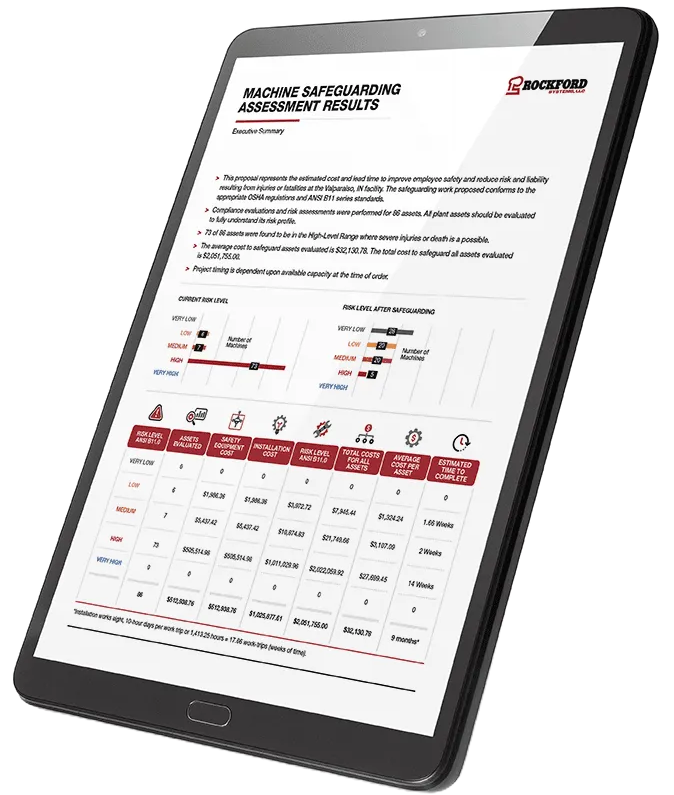
Schedule Your Annual Validation Audit Today
Our expert team will perform a comprehensive audit, including visual inspections, document reviews, function testing, and compliance checks to identify any gaps in your machine safeguarding systems. After the audit, you’ll receive a detailed report with recommendations for corrective actions to ensure your equipment remains compliant and safe. Protect your safeguarding investment today
Building a Safer Workplace with a Machine Guarding Program
A machine guarding program is essential for workplace safety, ensuring compliance with OSHA regulations and protecting employees from machinery-related hazards. Due to the complexity of modern equipment and compliance requirements, a structured program helps standardize safety measures, provide employee training, and maintain long-term safeguarding through annual audits. Key elements include compliance evaluations, written policies, implementation strategies, and ongoing training to create a safer, more consistent, and sustainable work environment.
Comprehensive Safety Solutions
Rockford Systems offers a full range of services to help businesses maintain compliance and create safer workplaces. Those include:
Training and Education
Safeguarding Policy Development
Machine Safeguarding Assessment
Remote Safeguarding Assessment
Emergency Response Assessment
Custom Design and Engineering Solutions Integration and Installation
Annual Safeguarding Validation Audit
Technical and In-Field Support
Annual Stop-Time Measurement
Press Safety Inspection